Billy's Make & Mend: Vintage Sewing Machines
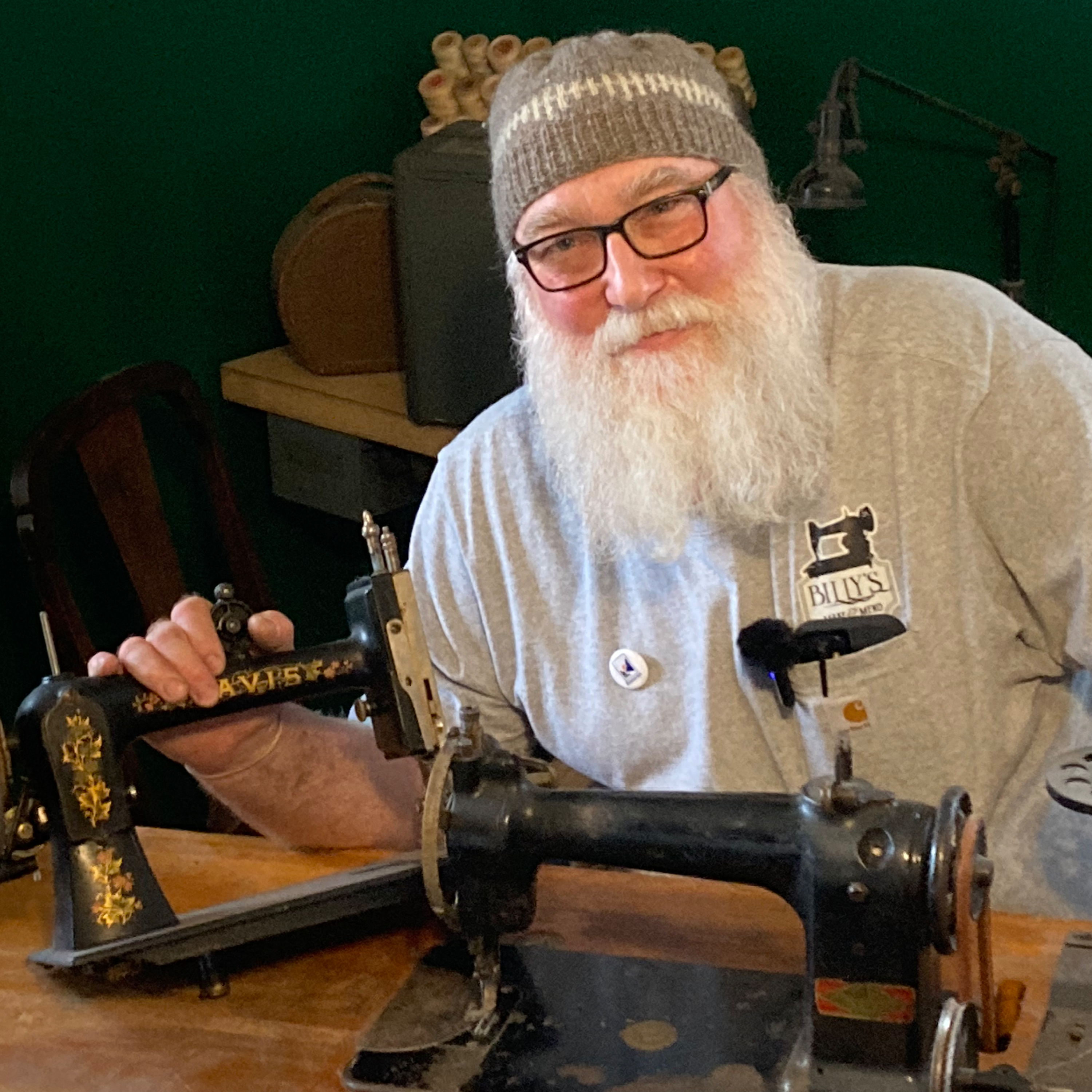
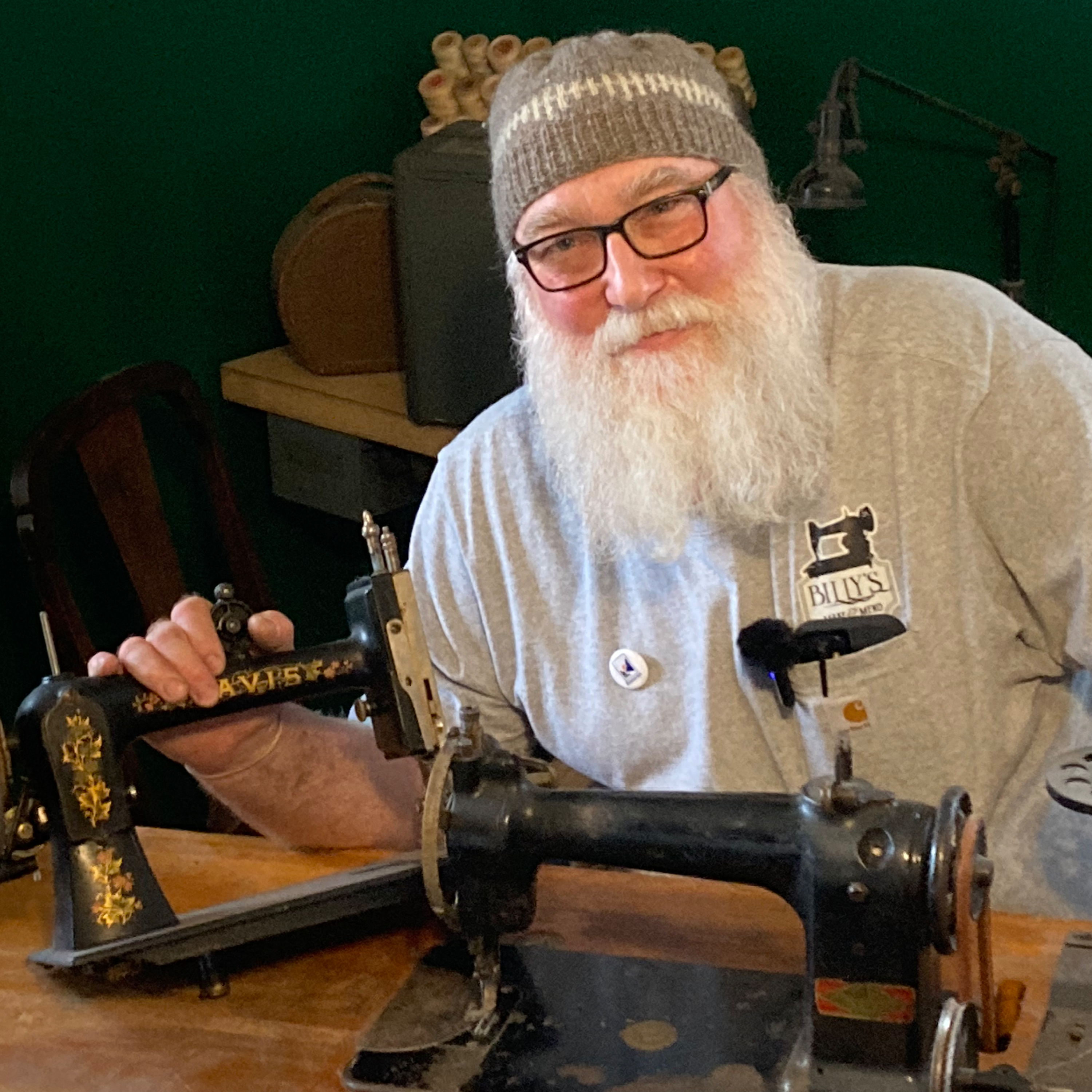
There's a "herd" of sewing machines in the hundreds, in Delancey, NY, and they're in the loving and capable hands of one Billy Hancock, owner of Billy's Make & Mend, an outpost for sewing machine repair and maintenance, sewing work, machine lessons, and plenty of history.
Thanks to our latest sponsor, Ulster Savings Bank, which was established the same year as the Singer sewing machine company, 1851! Thanks also to the continued support of the Catskill Mountains Scenic Byway and The Mountain Eagle.
--- Support this podcast: https://anchor.fm/kaatscast/support
Billy Hancock 0:03
The clickety clack and the sound of the belt over the pulleys and the feel of it when you're moving it with your feet, it's hypnotic. When I'm sewing with the treadle machine or an older machine, it kind of gets you into a trance of sorts and it's wonderful because everything else disappears.
Brett Barry 0:23
At Billy's make and mend in the western Catskills, Billy Hancock tends to hundreds of vintage sewing machines, repairing, maintaining, instructing their users, and of course, sewing. We met up at his shop in Delancey, New York.
Billy Hancock 0:41
Hi, everybody in radio land or podcast land I'm old. I'm Billy Hancock, and we are at Trilliam acres. The fun name we call our property here in Delancey. It's our power couple name. I'm Billy and, or William and my wife is Tracy. So it's Trilliam. Tracy and William. We've been up here for it's going to be five years in August. And we absolutely love the Catskills. We love Delaware County. We love Delhi. I am a sewing machine. repairmen and 57 years old father of three boys, Navy veteran, and happy to be up here we're in heaven.
Brett Barry 1:20
How long have you been working on sewing machines?
Billy Hancock 1:22
So I've been doing it as a business for approximately three years, little more than three years just after we moved up here. I started my business up here, but I've been collecting for about eight years when I got the bug was when my wife Tracy and I were having a garage sale and our friend Susan joined us and she brought this dingy green singer case with her and I said Susan what's in the case? She said it's an old Singer sewing machine. You don't want that thing. And I said let me see it. I opened it up in the thing was a tank all metal beautiful mint green. There was a 15 125 singer for those vintage sewing machine nuts out there. It was my first vintage sewing machine. I bought it from her for I think it was $40 I played with it, started sewing on it. And then I started delving into the history of Singer sewing machines, Isaac singer, all the other manufacturers, there's the sewing machine wars. It's just an incredible history. I started learning about the rare remodels and some of the other functions. I started sewing seriously and doing repairs and putting things together for friends and family and I started collecting so before moving up here to the Catskills. I think I amassed over 200 Both household and industrial sewing machines in our little Cape Cod house in Pearl River, New York. Also borrowing some space at my full time job party moving up here which was in property management. I borrowed a couple of basements of the apartment buildings that my boss kindly let me use for some storage before getting getting them all up here. It was quite a move.
Brett Barry 3:04
So in the span of about seven years, you went from from one sewing machine to,
Billy Hancock 3:10
to 200. Mmm, maybe, I think I'm at 250 now and the main herd is down in the basement. We're very lucky to have a big basement and the center area is going to be an industrial sewing machine workshop down there and my main storage but I have some cherry picked rare and beautiful and useful machines up here that I work with. And also I let people use my shop for sewing.
Brett Barry 3:36
So the collection ramped up very quickly.
Billy Hancock 3:39
It ramped up pretty quickly. I got bit hard. Yeah.
Brett Barry 3:42
And where did you get all the machines?
Billy Hancock 3:44
So I'm a big fan of garage sales, estate sales and Craigslist. Being down in the Rockland County Bergen County area, it was prime picking for all of these machines, people were selling them at $25 $30 a pop. And I soon got a lot of really nice machines and some rare ones down there. Knowing, you know, I was basically formulating my business plan for up here where I was able to I wanted to provide restored renovated vintage sewing machines to folks up here in the Catskills because I believe that the vintage machines are much better made than anything you could find now, and they all have a lot of the same functions that are used 99% of the times by Sowers which is your straight stitch and reverse your zigzag and your needle position. Sometimes you'll have the need for an elastic stitch. That's 99% of anybody's sewing really. I quickly gathered as many of those as I could to bring them up here and you know, I'm basically getting my money's back plus my time put into restoring or renovating, getting them back to sewing factory new when I sell them.
Brett Barry 4:53
And what brought you up here?
Billy Hancock 4:54
My wife Tracy and I got married in '05 and she had the brilliant idea of coming up to the Catskills for our first anniversary in '06. And we started staying at Kate's lazy meadow on route 28 in Mount Tremper, which sadly is no longer and they were also dog friendly so I was able to bring my blue heeler up and go trout fishing in the morning on the esopus which it abutted and we just fell in love with the Catskills. We came every year for about 14 years before deciding when our youngest son was starting college. We sold our home in Pearl River, New York and bought this beautiful house and property here in Delancey.
Brett Barry 5:38
So tell me about Billy's make and mend everything that you do.
Billy Hancock 5:42
Sure. So the term is a naval term. I'm a Navy vet. I think it started with the Royal Navy, the British Royal Navy had set aside some time or a whole day it was usually Sunday, where sailors were able to make and mend their uniforms, their clothing, their gear, and I love the term. So I decided to make it my business name Billy's make and mend. What I basically do is mainly sewing machine repair. I'm very popular with the quilting ladies up here and gentlemen up here, some of the quilting guilds in the area. And as far away as Oneonta, they've asked me to come and do programs for them, which is just basically a lecture talk about sewing machines. And I bring some of my prize jewels there to show off on the table and let them play with and talk about maintenance and servicing and what I do and normally when I leave there, I have a couple of ladies pull me aside and say, You know I have three machines in the car if you don't want mind taking them and throwing them in your truck and you can get them back to me or I'll come pick them up. And they've been so kind to me so generous with giving me work. I was shocked when I first came up the number of sewists up here, seamstress, sewist, tailors alteration people and I only really advertised the first year of that I started my business after that word of mouth just caught on and I have people coming to me from an hour and a half away. They don't want to go to Albany, they don't want to go to Binghamton. Plus, I have a kegerator here and you can have a nice, cold brew while you're talking with me about the machine and what needs or cup of coffee, hot cup of tea. I like people to feel welcomed here and comfortable. And I've just been very blessed with really great customers and a lot of repeat customers and people getting the word out about my business. My other part of my business is of course, sewing machine sales and I only will sell machines that are vintage, mid 70s And earlier that are all metal and that don't have computers. They don't have servo motors and micro switches and all those little things that can go bad. And once they go bad the machine is almost totaled because the amount of work that's needed to get that part back in the guts of the machine. I also do sewing jobs. I like the heavier stuff. I find it a challenge to put together tops for boats and jeeps and tractor covers and doing mending. It's fun for me, it's a challenge for me. Most recently, my wife and I being huge allies to the LGBTQ plus community and also being in the Delaware County pride group. We have gotten to know a lot of queer folks and a lot of drag queens in the Oneonta area. I'm working right now with a wonderful, fantastically talented drag queen named Lily Bola who asked me to work with her to get a wardrobe together for a pageant that's coming up in March. And I'm super excited to do that. It's my first time doing something of this nature and being a fan of drag and Lily Of course, I'm probably her biggest fan. It's just like a dream come true. And I'd love to have more drag queens, see what we're doing here and and get some more wardrobes, costumes, whatever you want to call it together for them. Hopefully help them out and I do some business.
Brett Barry 9:03
Tell me a little bit about the history of the sewing machine. How did it change how we dress and live? You know, what were you doing before sewing machines?
Billy Hancock 9:14
Well, before sewing machines, we were hand stitching, it took up a huge amount of time and it was tedious. The sewing machine was a disruptive industry it was a disruptive invention, meaning they found something that did a job in such a lightning quick way from the previous mode that it just changed the world really, I believe Gandhi once said it was the only machine that he really approved of or something like that, where he said this is liberating. It's liberating for women. It's liberating for people and he also sewed so in the beginning when sewing machines first emerged, there were several inventors that came up with a lock stitch machine. That's your basic first stitch that was developed and was the breakthrough. It enabled a needle to pass through the fabric loop around the bobbin case or carriage, using a hook and forming a lock stitch, essentially doing a job that was normally done by hand in infinitesimal amount of time comparatively. The sewing machine inventors were all competing against one another. And Isaac Singer was a brilliant man. But he wasn't an original guy. He took something that someone else made, and he made it better. He was a brilliant businessman as well. His was the first company that started the layaway plan, people were able to take a look at this machine, which was like six months salary for their husband, and they were able to put, you know, $2 a month towards it and pay it off. So he sold millions of machines in his own lifetime, and countless others afterwards.
Brett Barry 11:07
He was a bit of a scoundrel to wasn't he?
Billy Hancock 11:09
Well, Isaac Singer was a scoundrel and he had many mistresses. He was really outcast from American society and ended up living in England, where he had his last mansion built. American society did not like the fact that he had several mistresses and many children with those mistresses. And he was just carrying on like business as usual. But he was really shunned by the high society. He was one of the richest men in the world, yet, he was an outcast. He was he was a character. When he passed away the court battles were epic. Talk about a nasty, nasty time in the courts with all the Mistresses and wives and ex wives coming out of the woodwork and the children. He left quite a legacy in many ways.
The first working sewing machine that was practical for sale and mass production was the singer model one in 1851, when singer manufacturing company Simanco was formed. And right behind you behind my shelf of repairs, there is a singer model three that was built in 1861. The black one in the back behind the shelves there. Yeah, that's a museum piece. Really. I found that here up in the Catskills. It's still working, it's gear driven. You can't kill them. It's a cast iron and steel. And they're oil thirsty and they need some grease and rust is their enemy. But you can defeat rust, you can clean up rust and get it going. Again, if you do find one that's in poor shape. That machine there is one of my crown jewels and I can't move it anywhere. It weighs a ton. That one was used for sewing the tops for horse and buggies. And also at the advent of the invention of the automobile. They did the rag tops for convertibles, and they were still used for 100 years after they were made. That still works.
Brett Barry 13:17
Now right in front of that one, I see some modern machines, it looks like you repair modern machines to
Billy Hancock 13:22
I do and what I what I do with the modern machines is I will clean them. I will check timing and tension. When it comes to modern machines that have those little servo motors and micro switches and motherboards and such. I tell folks straight up when they bring them to me if there's an error code, you're best off sending it to the dealership and let them do it because they have the diagnostic tools to see exactly what it is. And you may be charged an arm and a leg but they're gonna fix it quicker than I could by swapping out parts to find the problem. I don't do that. I don't think that's fair to the customer. If I just keep buying parts until I find the one that's not working, they will bring them to me for cleaning. And for checking timing and tension which I could do to any machine really.
Brett Barry 14:10
How do you find parts for the vintage machines
Billy Hancock 14:12
Believe it enough for a lot of the older machines, there are still parts available used parts. I will also take donations and have bought machines from garage sales, estate sales and such that I will cannibalize for parts to keep the better machines that are in better Nick running and working for their owners. And I'll just keep stripping every little screw and bolt and spring off of them to keep something else running and I'm keeping machines out of the landfill. I've got the space for it down in the basement and you know eventually what I'm left with nothing that will go to scrap. So I don't like putting anything in the landfill.
Brett Barry 14:51
Have you seen a resurgence in interest in sewing and I would think that maybe with even the pandemic people being home and also just then Need in the beginning to sew your own masks? Probably Probably a lot of machines came out of attics and basements and closets.
Billy Hancock 15:06
Exactly right. Coming up here, I was surprised at the number of sewers that were up here I was thinking that we'd have a slow start. And once word got out, it wasn't like that at all. It actually came in waves. When the word got out to all the quilting guilds that I was here. While nobody had to go to Albany or Binghamton anymore, they came here, which was 30-40, you know, an hour away, instead of going up to those big cities. Once the pandemic hit, I had mask makers coming to me. And I would also free of charge, do zoom calls with folks who are far away and needed help getting their sewing machines running again, or if they had issue with it, I could walk them through whatever it was, I just wanted to donate my time and my expertise for these mask makers who are donating their masks to first responders and medical professionals and these mask makers, unfortunately, some of them Well, fortunately, and unfortunately, they would pull a sewing machine out of a closet that have been sitting there for 15, 20 years, dry as a bone, the poor thing, throw it on their kitchen table, start sewing away like the dickens and all of a sudden they hear a clunk. "And Billy, I heard this horrible noise". And I would say to them, yes, that is your gears dying inside and those plastic gears of your 70s or 80s or 90s machine that you haven't done anything with and you should have cleaned it oiled and you know, I could have done this with you over the phone or through zoom call. Let me see what it'll cost. And a lot of times, unfortunately, with the machines with plastic gears, the machine is totaled, buying the gears and then the labor that it takes me to take the thing apart and replace those gears, the cost of the machine is eaten up right there. So it's better to just run out and grab either a new one or hit a garage sale estate sale, grab a machine and bring it to me or get on a zoom call with me and I'll show you how to do it, how to clean it how to oil it grease it so that you can get a few miles out of it still, but mask making was a huge boom. But even after that you have people who were home more and they wanted to pick up a hobby. They wanted to hem their own jeans, they wanted to shorten those curtains that are dragged on the ground or on the floor in their living room. And so they started picking it up and asking me what machines to purchase if they're buying new or I would offer them a machine that I might have an inventory that would do all the sewing that they would need.
Brett Barry 17:34
Would you like to show me somebody for your machines or some of the work that you're doing at the moment?
Billy Hancock 17:38
Sure.
Brett Barry 17:39
Great. Stay tuned for some highlights from Billy's herd, but first, in 1851, the same year Singer Sewing Machines was established. So too was our newest sponsor, Ulster Savings Bank is a local bank with a long history of serving the community and offering the modern conveniences of online banking. Visit their locations in Phoenicia and Woodstock, Call 866-440-0391 or visit them at Ulstersavings.com Member FDIC equal housing lender. Kaatscast is also sponsored by the 52 mile Catskill Mountains Scenic Byway following New York State Route 28 through the heart of the central Catskills for maps, itineraries and links to area restaurants, shops and accommodations. Visit sceniccatskills.com and buy the mountain Eagle cover in Delaware greene and Schoharie counties, including brands for local regions like the Windham weekly schoharie news and Catskills Chronicle. For more information, call 518-763-6854 or email, mountaineaglenews@gmail.com. Back at Billy's Make and mend in Delancey, New York, Billy jokes that he has a hoard or herd of sewing machines, about 250 of them in various states of operation. He showed me quite a few of them. And here are some highlights from that tour.
Billy Hancock 19:10
Well, we could actually start right here. And behind me is one of my go to sewing machines, but also one of the crown jewels of Billy's make and mend and it's the singer 431 G. And the G denotes that it was made in a German factory that is no longer and that machine was made in 1965. It was only made for one year and it was the pinnacle of the vintage Singer sewing machine design and engineering. What makes this machine very special number one is the German factories, their machining tolerances were very tight. It's a very smooth machine, everything built very well on it, but it does a whole host of functions. It has built in cam stacks, which means you're able to do embroidery stitches that are already built into the machine. All mechanical, no computers, no micro switches, no servo motors, one motor, and all metal except for some plastic where it's acceptable never in the gears, you don't want plastic gears. If we come over here, we have a lovely Dookie Baby Lock. The EA 605 serger, which is a brilliant machine made I believe in the 70s. I have a couple of these because I sought them out because they're all metal machines they sew beautifully. They're highly portable. And they're just brilliantly made. Look at that beautiful green Come on. This is a machine that a customer just brought to me today. This is the elna Supermatic a wonderful machine and actually brilliantly designed, there was a Spanish gentleman who was unfortunately caught up in the Spanish Civil War, he came up with the idea of having a sewing machine manufactured that would be good for people on the run, unfortunately, refugees and such needed to have something that was portable. And if they're moving around to get away from the fighting, they would still be able to mend and make their clothing and household goods, whatever they needed. So he came up with one that was the element number one, also nicknamed The grasshopper, and much like the elna Supermatic, it had designed with it a carrying case that turns into a tabletop sewing machine bed. So when you take this cover off and put it on a table, it acts as your work surface. But when you take the case or the cover off of the machine, you have a free arm sewing machine so you can more easily sew hems and cuffs and such and sleeves, brilliant machine, all metal has a cool function where you can actually put a knee lever in a shaft in the machine. And when you have the machine at the edge of the table, you're using your knee to actuate the motor. So highly portable, all metal, you can't kill them. And again, they're oil thirsty and just a brilliant design.
Brett Barry 22:17
What are you doing to it?
Billy Hancock 22:18
This is an unknown animal, I have no idea what's going on with this. So that'll go on the workbench and I will first clean it and inspect it. And check the motor, check the brushes, all that good stuff, make sure that everything's there before I start it up. Because you don't want to fire up an old machine without first making sure that nothing is going to bash into something else and break something. Because parts are hard to find a lot of times because they're all metal and very little happens with them unless it was dropped. It'll start right up. And I'll give it some Billy love with the oil and the grease and all the best products that I can find to put into it and check the timing and tension. And then I'll sew it off and I'll leave my sample sewing patch underneath the needle. So the owner when they pick it up and bring it home, they see that I did every stitch that this machine can do. And they can do it too. And if they start fiddling around with the bobbin tension, "oooooh" just don't touch the Bobin tension people, please that's my biggest pet peeve is people who want to play with the Bobin tension. Did I mention Bobin tension, I'll get her sewing to like Factory New, make sure the tension's right and give them a little heads up on the operation of the machine if they've never used it before. If it's a new acquisition for them. I'll give a little history if they're into it. A lot of people like to hear where this machine came from and who designed it and what it was meant for. What we have here is the singer 29 4 this machine was called the cobbler still called a cobbler. This one is kind of rare, because in the US we didn't have the hand wheel along with the treadle base that normally the machine was sitting on. And what's really ingenious about this machine is the presser foot which presses down on your fabric. It actually is omni directional, you could turn it around 360 and your work will be moved in any direction. So it's much easier to work in tight spaces on this machine. This machine can go another 100 years. The sound to me is hypnotic when I get a treadle machine going, when you're using a treadle, the clickety clack and the sound of the valves over the pulleys and the feel of it when you're moving it with your feet. It's it's brilliant. It's hypnotic. When I'm sewing with a treadle machine or an older machine, it kind of gets you into a trance of sorts and it's wonderful because everything else disappears and you're just concentrating on your work which which is the fabric your work is the fabric that's under the needle, under the presser foot, and you're, you're a one with the machine. So I really enjoy sewing in on many different machines. This one is kind of brilliant because the drawer is still attached to it, you don't find them with the drawer. Here we have right next to our 29 4 is a 246 3. And what I also love about finding these machines is the history that came with the machines. This machine came from a woman who her whole life was working in a clothing factory, using this machine, mainly manufacturing wedding dresses, and such high end garments. She was an expert at this machine. This machine it was offered to her from the factory. And I found that a lot of the times when people retired from these clothing factories, they were offered their machines to buy them to bring them home, to use them in their little cottage industries and keep selling if they wished. And a lot of people did do that. So she kept making prom dresses, wedding dresses and such with this machine. Until she was done. She was just done and said you know it's going to someone who's going to use it. And you know, a lot of people are very happy knowing that it's coming to a shop where it's still going to be used, not just turned over and flipped or sitting there. It came in its original table with original motor with original lighting. And it also has the offshoot the little ramp where the cut offs from the surging process went into a wastebasket right next to it. So I've never seen one like this. And it was just brilliant to find it in this in this condition. Here's another brilliant machine right here, the singer bar tacking machine, that's the machine that will form those reinforcing stitches on your belt loops on your jeans or pockets. And this is one of those specialty machines where you don't see every day. Even fashion designers and people who do high inventory or make a lot of clothing. They won't have this machine a lot of times in their shops. So I offer my services and my machines that do these specialty stitches to local folks and designers to do production runs if they want. That one is a 240 volt. So I had our wonderful electrician run a line specifically for it in my shop and so she will live here, right there forever. This machine here is Wilcoxon Gibbs high speed sewing machine which has a brilliant rotary take up lever in the front of the machine one of the fastest early machines ever made. This I actually bought from the original tailor who bought it when it was new. His whole life was sitting at this machine. Some machines have amazing histories and some of the things that I find inside the cabinets and drawers are very personal mass cards, notes to friends and family. The folks that I normally buy these from will sit and tell and I'll take all the time in the world. I'll sit and listen to the whole story behind the machine. And I'll remember most of it. This this gentleman, unfortunately had Alzheimer's in his later years. And so he was not very communicative when I met him. But I'm just amazed by his history and the amount of work he did with this machine. You see the wear on the table and the bed of the machine where paint is missing. That's miles and miles of stitching. His wife was so proud of him. And they knew that this was going to a shop where it's going to be loved and used. And it's just super fast and scary. And I love it.
Brett Barry 28:47
Where was this Tailor based?
Billy Hancock 28:49
He was out of Lodi New Jersey.
Brett Barry 28:51
Could we hear it?
Billy Hancock 28:54
Yeah. If you don't mind me taking a second Yeah, firing it up.
So most of the older machines had what's called a clutch motor. And the clutch motor means that you have an actual clutch that will engage the motors pulley with the belt which runs up to the hand wheel of the sewing machine. And so it's kind of going like from zero to 60 in three seconds if you're not used to it. So I always caution people who get older machines that run with a clutch motor to start off slowly get a block of closed cell foam to put underneath the tredle of the motor controller so that it will regulate the pressure a little better than doing it by foot. So this is this is gonna go now
So if you feather it, that's when you first start out, go nice and easy. Then when you're doing long straight runs, you put the pedal to them.
This is one of the fastest sewing machines made. I think it comes out to 6000 stitches per minute. But brilliant machine, obviously miles and miles of, of sewing done on it, but you can't kill them all metal
Brett Barry 30:38
I would imagine that the machines that are used industrially and like a shop in Bangladesh now because we don't do it here in America anymore, would be closer to this quality, heavy metal kind of made to be used.
Billy Hancock 30:52
Correct. And they're much more expensive as well. The manufacturers know that they're going into a shop with high production. And they know that only all metal machines can put up with that. You know, a Volkswagen Beetle can do 100 miles an hour for a short amount of time. Can it do 100 miles an hour? Yes. Do you want to do that all day long? In a Volkswagen? No, because it's gonna kill it can a Ferrari do 100 miles an hour all day long? Yes, because it was built for it. When I have people come to me with their sewing machine. And they say I want to make jeans with this household sewing machine. And I say to them, well, you're gonna make a couple of jeans with this household sewing machine. But you really want a semi industrial or an industrial machine if you're going to do production.
Brett Barry 31:36
So you can still get a modern machine, but it has to be an industrial machine, of course, be all metal.
Billy Hancock 31:41
Sure, there's several manufacturers that are brilliant, and still making, you know, have always made industrial sewing machines. And they're readily available, but they come at a very high price. They're very expensive. Here's another industrial, another singer industrial early model. I would say this is from the I want to say the 40s and another beautiful upholstery machine. And I actually have a customer who's looking for this machine to make wallets locally, with locally sourced cowhide, and he's starting up a business.
Brett Barry 32:14
Wow, that's cool.
Billy Hancock 32:16
Yeah.
Brett Barry 32:17
You going to sell him that wonder find another one?
Billy Hancock 32:19
See, that's the problem because I fall in love with the machine. And if I have only one of it, I kind of want to keep it for myself and love it and sew with it and use it, and then I'll sell my doubles of machines that I find. But this gentleman, he is worthy. He He's a really passionate guy with his craft. And so when it's going to a good home, I don't mind I guess it's almost like people who have puppies or kittens. You want to make sure it goes to a good home. So I know this would go to a good home, but I will miss it.
Brett Barry 32:56
And so if anyone wants to get a machine repaired or wants to buy a machine and wants to learn how to use the machine or any of the other services that come with Billy's make and mend, how do they find you?
Billy Hancock 33:10
So you can find me on Facebook Billy's make and mend Facebook page, you can text me or call me at 201-723-9228 Yes, I'm a Jersey boy and I will never get rid of my jersey cell phone 201-723-9228 That number again. 201-723-9228 you could also email me at BillysMakeandmend@yahoo.com all spelled out or pop up to the house and have have a have a brew with me.
Brett Barry 33:40
Speaking of that brew
Billy Hancock 33:43
are we gonna have one, are we gonna?
Brett Barry 33:45
Do you make it?
Billy Hancock 33:46
No, no, I I used to. While I was still contracting. I was working also at a Brewing Company in Pearl River New York Defiant Brewing Company owned by the brew master fantastic gentleman named Neil Acer. his lovely wife Amy. I promised Neil that once we moved up to the Catskills that when I got my Kegerator I would only pour defiant Brewing Company beer out of my kegerator. And I've kept my promise almost five years now. And so right now we have a beautiful Pilsner and we have a beautiful IPA on tap here at Billy's Make and Mend. So you can come learn how to sell and have a brew or a glass of wine or a cup of tea cup of coffee. I like people to be comfortable and you know who doesn't like a brew in the middle of the day, sometimes?
Brett Barry 34:32
I do. And we did. And it was delicious. Thanks Billy. Kaatscast is a bi-weekly production of Silver Hollowm Audio, discover more kaatscast.com where you can search the episodes, join our mailing list, which includes photos from the field, or donate to the show with as little as $1 a month. I'm your host Brett Barry. Thanks for listening, and we'll see you again in two weeks.
Transcribed by https://otter.ai / AA